Maintenance Workers Are Not Part Of The Remote Work Revolution: How To Help Them Cope
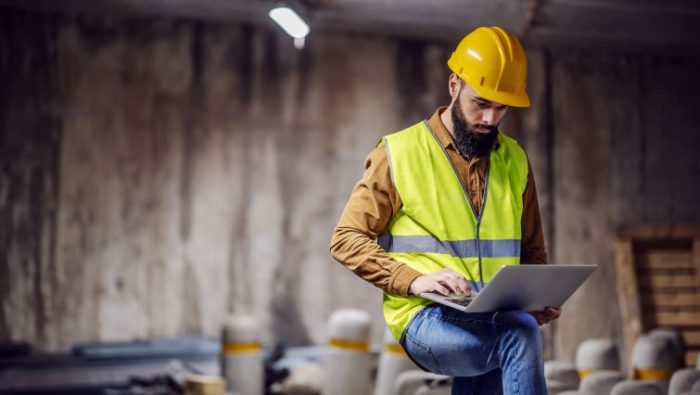
There has been an explosion in the number of people working from home over the past 18 months. Unfortunately, this type of work is not available to all. Due to the nature of their work, maintenance workers are not part of the remote work revolution. Company leaders in the maintenance sector must make extra effort to help employees cope with the remote work revolution and its side effects.
Remote work was here even before the pandemic but the spread of COVID-19 started a real remote work revolution. Also, relevant research shows that remote work is here to stay. According to Gartner, 82% of company leaders plan to allow employees to work from home at least some of the time.
But what about workers that are not able to take part in these new ways of working?
Maintenance workers in factories, vendors in grocery stores, transportation workers, construction workers… The list goes on and according to the Economic Policy Institute, less than 30% of these workers can work from home.
Plant managers must ask themselves an important question: how does their workforce feel knowing they cannot enjoy the benefits of remote working? Also, they have to ask themselves how to make this situation bearable for workers and help them to cope with the fact that the future of their work isn’t and is never going to be remote.
Invest in Workplace Safety and Health
Maintenance work is often hazardous. That explains the significant number of workplace incidents each year that occur due to maintenance work or other non-production tasks carried out on buildings, machinery, and equipment.
A European Union (EU) report indicated various studies proving that industrial maintenance employees are eight to ten times more likely to develop an occupational disease than the average worker. The main reason is a lack of proper occupational health and safety (OHS) management systems, as well as inadequate job-relevant and risk-appropriate training.
Injuries and deaths arising from maintenance-related work typically arise due to:
- an over-reliance on workers’ specialist skills;
- lack of proper supervision;
- lack of proper safety procedures and training;
- failure to ensure compliance to safety procedures; and
- prioritizing production over safety.
Safety and health management systems need to be diligently planned, implemented, constantly checked and maintained, and audited. Systems based on continuous improvement ensure that maintenance workers are safe and healthy while they work.
Increased Wages and Non-Monetary Benefits
Paying higher wages is an obvious way that plant managers and supervisors can help maintenance workers stay motivated. MIT professor Zeynep Ton, the author of The Good Jobs Strategy, found a clear correlation between higher wages, better productivity, and higher profits for those companies who paid their employees more, counter-intuitive as that may seem.
But workers don’t stay motivated solely because of money. There are other, non-financial incentives that maintenance workers can be offered to counteract not being able to do remote work. Overwork can be highly detrimental to worker morale, health, and wellness, for example, and so increased paid leave can be an excellent recharge for a worker.
Recognition of work well done is another way of providing motivation. Flimsy certificates or cheap platitudes are not the way to do it, however. Recognition, even if non-financial, needs to make a tangible difference for the employee. Offering a visit to a luxury day spa is the type of recognition, for example, that makes a worker feel good about their work and their employer.
Invest In Training and Upskilling Your Workforce
A well-trained and skilled workforce is a smarter, more resilient, and more loyal workforce. This is particularly true of the maintenance workers who always must know what they’re doing and who can work well under pressure. Employers need to actively encourage learning in the workplace, including online learning options.
Employees crave upskilling – an Accenture survey on insights into the future of work found that an astonishing 95% of employees believed upskilling was critical to keeping them relevant in the workplace. As Accenture notes: “Leading businesses are reimagining the nature of work, pivoting their workforce to create new forms of value and scaling up ’new skilling.’”
Cross-training between different skill-sets or types of technical knowledge, for example, is another way of ensuring workers remain well-rounded in their work. This is especially relevant for maintenance workers, given how flexible and multi-faceted they often need to be in their day-to-day tasks.
Build a Digital Infrastructure
It is a mistake to consider maintenance work as primarily ‘manual’ and, therefore, ‘non-digital’. All work and, in particular, work processes are becoming increasingly digitized in literally every industry sector. Digital transformation is here and even though maintenance workers are not part of the remote work revolution, they are certainly are not immune.
Facility managers are increasingly adopting software tools such as computerized maintenance management systems (CMMS) in order to have smoother-run maintenance systems in place that are both resource- and cost-efficient. Maintenance workers are often an integral part of the success and practicality of these digital systems.
Digital infrastructure can be even more sophisticated in what McKinsey & Co. calls “digitally-enabled reliability,” which goes beyond typical proactive or even predictive maintenance. Advanced predictive maintenance (or PdM) is a result of the so-called digital ‘Fourth Industrial Revolution,’ whereby artificial intelligence (AI) and machine learning (ML) can warn operators and those in maintenance well in advance about potential breakdowns of machinery or equipment.
The ramifications of this technology are immense in terms of acquired skills and improved safety and health for workers.
Healthcare Coverage For All Workers
Many American workers are anxious about their healthcare coverage, especially given how the United States has the highest private healthcare costs in the industrialized world. Maintenance workers may feel particularly vulnerable given that they often do hazardous work that could injure them and may not earn enough to afford a premium HMO plan.
The Sanofi Canada Healthcare Survey results confirm that a workplace environment or culture that supports personal health and wellness provides dividends to employers as well as employees.
An employer with a genuine interest in retaining its maintenance workforce would do well to consider comprehensive healthcare plans that include:
- Greater scope of healthcare coverage
- Flexibility and appropriateness
- Free yearly physical examinations
- Access to mental health services
- Easier access to paid sick leave
- Prescription drug coverage
Asking for Feedback
There is nothing worse in an organization than a lack of communication. In the words of the famous Irish playwright George Bernard Shaw: “The single biggest problem in communication is the illusion that it has taken place”. Equally as bad is communication that is only one way, i.e. top-down.
Two-way communication between management and employees allows for feedback from employees that can inform decisions made by plant managers.
Good, open communication means that work can be done efficiently and safely. This is especially relevant in the maintenance industry, in which workers are often ‘out in the field,’ working alone or in small teams. They need to be freely able to communicate their issues or concerns regarding processes, procedures or equipment to their line management.
A growing trend is to avoid conventional feedback, such as annual or quarterly performance reviews, which are often dreaded by all. Instead, providing less formal and more regular ‘check-ins’ with workers can help increase productivity and lower performance anxiety.
Key Takeaways
Employee retention is at the heart of this article. Managers need to remember that not being able to enjoy the flexibility and benefits of remote work can be hard on maintenance employees and may impact retention. Solutions provided cannot solely be offering swanky work benefits or implementing shiny digital platforms. Solutions must be holistic and intelligent to retain maintenance workers.
Ultimately, plant managers and supervisors need to remember to:
- Make safety and health a top priority;
- Train, upskill, train, upskill!;
- Provide work benefits of different types;
- Think digital transformation;
- Offer good healthcare; and
- Ensure open communication at all times – without fail.
Even though maintenance workers are not part of the remote work revolution due to the nature of the job role, it is still possible to change and adapt to help meet their needs.